2016 Biesse Stream B1 8.0 used edgebander #BBM2649
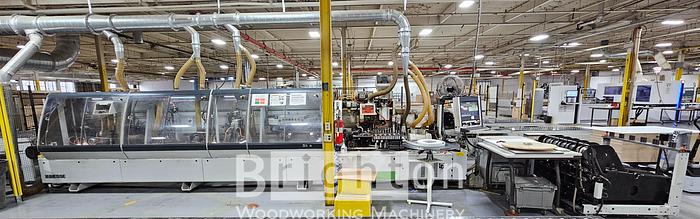
2016 Biesse Stream B1 8.0 used edgebander #BBM2649
Location:Ontario, Canada
Description
*Reduced Price* 2016 Biesse Stream B1 8.0 used edgebander
For pricing please click “REQUEST QUOTE” wherever you see it on our Brighton Woodworking Machinery website at www.brightonmachines.com.
Click <LEASE> for leasing information
Click <SHIP> for shipping information.
Specifications
Manufacturer | Biesse |
Model | Stream B1 8.0 used edgebander |
Year | 2016 |
Condition | Used |
Stock Number | BBM2649 |
Quality | Very Good |
Electrics | V / Ph / 60 Hz |
Additional Features
2016 Biesse Stream B1 8.0 used edgebander
Input/Output
Feeder guide adjustable according to the machining edge being used, with mechanical digital display.
Base
Base made of electrowelded elements stabilised to form a single, monolithic, high-rigidity structure.
It rests on the ground on a suitable number of cross-bars, each of which is fitted with adjustable feet and set up to be anchored to the floor.
Auxiliary suction and dust collection system along the base, with D.160 suction mouth on one side of the machine.
Drive chain
The drive chain comprises a high precision, minimum distortion chain (50.8 mm links). Free, straight advance is guaranteed by the presence of guides, which are round on one side and flat on the other, both tempered and rectified, housing slide blocks made of technopolymer and self-lubricating material.
The panel rests on high grip, rectified, stain-proof rubber tables.
The speed of the drive chain is continuously adjustable from 10 to 25 m/min by inverter controlled directly from the NC, with rapid braking function.
The drive pinions are made of heat tempered, high-strength steel.
Belt presser
The top presser comprises a rubber belt with a stain-proof coating. The thrust exercised on the panel is provided by springs housed on technopolymer connecting rods. The whole assembly is fitted on a extruded aluminium structure, whose section guarantees high rigidity.
Sound-proof cabin for edgebanding section
All the units fitted with rotating tools are located inside cabins coated with sound-proofing material. During machining, the units can be viewed through wide, transparent polycarbonate windows.
If the doors are opened at unauthorised times this will trigger an emergency and shut down the machine. Internal lighting provided by anti-glare neon lights.
Suction hoods of each unit are connected through pipes to individual exits placed in the upper part of the cabin. The cabin of the side to be shaped is equipped with panel cleaning device.
Mechanical panel spacer
Device allowing manual introduction of panels only when the distance between panels is enough for working. Distance between panels is set up on NC.
Piece support
Side piece support supporting the panels as they pass through the machine. Fixed supports, nr. 1 manually adjustable roller bar.
PC Numerical Control
Multiple axis numerical control with PC interface for management of single edgebanding machines or complete edgebanding lines.
Main software characteristics: Windows operating system
Sintra machine control software, based on Windows like interface. Electronic axes positioning (machine set-up).
Electronic feed chain speed adjustment.
Electronic presser height adjustment according to panel thickness. Automatic management of edge banding coils exchange device.
Management of machining list.
Automatic management of coil magazine by codes. Cascade type motor start-up.
Management of diagnostics.
Teleservice
It allows an immediate and direct access to the machine numerical control via network.
In this way it is possible to check machine data, user programs, input/output signals and system variables, and to install software updates, therefore granting:
Real-time service intervention. Quicker problem solving.
Consistent reduction of machine downtime. Real-time software updates.
* The teleservice support is free of charge for the whole warranty period.
NC Y AXIS FOR FEEDER GUIDE
The kit includes motorised movement of the machine feeder guide and relevant NC management.
KIT FOR AUTOMATIC PANEL OUTFEEDING ON LENGTHWISE AND CROSSWISE RUN
Multibelt device for single-sided edgebanders panel outfeeding, inline installed. It is suitable both for lengthwise and crosswise run.
Cod. N0000476 required.
KIT FOR PANEL SUPPORT STREAM B IN LINE, CROSSWISE RUN
Extension of fixed crosswise supports bearing panels with length up to 3200 mm and 4 bars with additional rollers.
U-SHAPED AIR TABLE AT THE MACHINE INFEED
Thanks to air table it is possible to handle big panels dimension at the machine infeed.
Electric fan power 0.75 kW.
PRE-MILLING UNIT RT30
Milling unit comprising two vertical axis motors equipped with slide copier, side adjustment and timed pneumatic drive.
The unit can be adjusted manually according to the panel overhang by digital position indicator.
It is possible to use this unit also without copier on the first motor. This avoids the adjusting
according to the removed material.
Maximum workpiece thickness with standard tool: 40 mm on Stream B; 60 mm on Stream B MDS 2.0.
On Stream B, for panels with thickness up to 60 mm, it is necessary to use diamond tool with height 63 mm (cod. N0001322 or N0000336).
TECHNICAL DATA
Description Um Min Max
Tool rotation speed RPM 9000
Motor size kW 3.5+3.5
Shaft (diameter x length) mm 30x50
Tool dimensions (diameter x height x bore) mm 125x43/63x30 (asymmetric)* Pneumatic drive stroke mm 10
2 dust hoods mm 80
Inverter Included
Tools provided DIA included
* Not compatible with postformed panels.
SPRAYING LIQUID APPLICATION UNIT
Device for the application of liquid using nozzles located above and below the panel. It can be used with the following liquid types:
Anti-adhesive liquid. Anti-static liquid.
Cleaning liquid.
Manual adjustment of nozzle direction.
ANTIADHESIVE LIQUID
Avoids the adherence of any glue waste on the panel surfaces.
NC ADJUSTMENT OF MATERIAL REMOVAL FOR RT30
NC management for the first motor copier, which determines the thickness of the material to be removed.
SUPPLEMENT PAIR OF SYMMETRIC DIAMOND MILLING CUTTERS FOR H=60 ON RT UNIT
Pair of symmetric diamond milling cutters 125x63x30 to replace the standard ones 125x63x30.
GLUING UNIT SP10
Gluing unit used to glue straight edges in coils in melamine resin, ABS, PVC, PP, veneer. Use of EVA-based thermoplastic adhesives
The glue is spread on the edge of the panel using a knurled roller. Main characteristics:
HighMelt patented system with separated glue and pot applications. Patented system for quick frontal extraction of glue pot, by rotating device. Patented HighMelt pre-melting device.
Shafts and reducers for the top handling. Glue pot and head Teflon coated.
Guillotine type batching device for glue roller, accessible from the operator side. Copier to optimize the glue quantity spread on the panel.
Sensor to detect the glue level inside the bowl.
Automatic start-up of the glue spreader roller on reaching optimum working temperature. Automatic disabling of the glue spreader roller on stoppage of the machine.
Glue spreader roller rotation speed electronically synchronized with the feed chain speed. Granule tank with vertical magazine fitted directly on the pre-melting device.
Edge presence detection device (using photocell).
Independent edge insertion/clamping device for each position (only with cod. N0000682, N0000683, N0000804).
Horizontal edge magazine for one coil.
Ability to change edge automatically - NC managed - (only with cod. N0000682, N0000683, N0000804). End of roll indicator light, with stoppage of movement if a panel is signaled and there is no edge (only with cod. N0000682, N0000683, N0000804).
Horizontal cutter to cut material in rolls: this is suitable for edge materials in: melamine resin, PVC, ABS,
PP, veneer up to 3 mm thickness.
Infrared Heater RP10: pair of infra-red lamps, top and bottom, used to heat the side of the panel to be edgebanded.
NC Y axis for presser section: the kit includes motorised edge banding strip presser section drive and relative NC management.
The pressing area includes:
1 presser roller D.150 driven by inverter. 3 idle presser rollers D.65.
TECHNICAL DATA
Description Um Min Max
Edge thickness in melamine and plastic mm 0.3 3
Maximum cutting section cutter mm² 135 (3x45)*
Panel thickness mm 10 60
Edge height mm 15 65
Edge length mm 250
Glue pot capacity kg 1.3
Tank capacity kg 7
Spreading capacity kg/h 7
Coil diameter mm 800
Z AXIS FOR EDGE GUIDE DEVICE ON SP10, SP20, SP30
Automatic adjustment of edge-guide height in proximity to the driven presser roller.
SUPPLEMENT 3 EDGE PRESSURE ROLLERS FOR SP10, SP30
3 edge pressure rollers in addition to the 3 standard ones in the gluing unit SP10 and SP30. The introduction of this option could require a longer machine size.
HORIZONTAL MAGAZINE FOR ONE SMALL DIMENSION COIL
Support circular plate not provided of residual length control device.
12 POSITIONS EDGE MAGAZINE FOR SP10, SP20, SP30, SP40
Twelve position container for rolls of edge banding strip.
The rolls are supported by a cradle of rollers, so that they do not require any other locking devices: this makes them extremely quick to replace. Automatic edge changement, NC managed.
Edge banding strip presence detection device (using photocell), also when the one working is finishing and the other is the same edge type.
Positioning of photocells for edge detecting device and for edge magazine can control a maximum panel length of 2700 mm.
To obtain the control of the edge roll ending on a panel longer than 2700 mm it is necessary to place the edge magazine at a right distance.
The distance (if different from the standard 2700 mm) must be communicated when ordering the machine.
GLUING HEAD FOR STRAIGHT EDGE
Glue application head complete with knurled roller with spreading batcher, resistance and thermocouple.
Application for straight edge.
System for pick-up of glue from the bottom glue-pot.
ADDITIONAL GLUE-POT
Kit comprising one additional glue-pot complete with resistors. 1 kg capacity.
END-TRIMMING UNIT IT90-S
Edge trimming unit complete with 2 motors, for edge banding strips with a thickness of up to 3 mm. Motors can be inclined on the vertical axis by between 0° and 25° with automatic rotation.
Device to move the trimmer away rapidly during operation. Kit 3 pneumatic positions.
Automatic disabling of the unit when motors are stopped. Central lubrication of slide guides.
Pneumatic drive of two end-trimming units. TECHNICAL DATA
FINE TRIMMING UNIT RF40
Unit comprising 2 independent motors, which are complete with horizontal and vertical copiers and swings on slides.
Vertical movement of the top unit associated with the belt presser. Continuous automatic adjustment of tool position with respect to the material using 4 brushless motors applied to the group drive.
The position is controlled directly by the machine control system.
In this way it is possible to use tools with a multiprofile on the unit, allowing the profile/shape to be changed without having to change the tool.
Automatic pneumatic exclusion of the unit from the control panel.
TECHNICAL DATA
Description Um Min Max
Speed RPM 12.000
Motor size kW 1+1
Panel thickness mm 10 60
Solid wood edge thickness mm 20
Shaft (diameter x length) mm 16x20
Inverter Included
Tools provided Excluded (Select requested tool)
2 KW MOTORS FOR RF10, RF30, RF40
PRO-NESTING KIT FOR RF10, RF30, RF40, RF12
Equipped with 2 bearing copiers in addition to the top vertical copier to permit processing of panels with holes up to diameter max. 35 mm and/or grooves. Distance between copiers 100 mm.
MULTIFUNCTION CORNER ROUNDING UNIT AR80
Unit for top / bottom panel fine milling and front /back panel corner finishing.
Complete with 2 ROTAX electrospindles swinging on cartesian axis to follow the panel copying. The unit moves on linear guides.
Movements on axis are performed by brushless axis motors.
NC controls the unit movement and the choice of the tool heads, if the unit is equipped with automatic toolchange device.
Operator interface is very easy.
The unit is equipped with 2 tool heads (one for each electrospindle). Electrospindle tool heads are equipped with fast pneumatic disabling.
TECHNICAL DATA
Description Um Min Max
Tool rotation speed RPM 12000
Motor size kW 0.65
Feed chain speed mm 25
Edge thickness mm 0.3 3
Shaft diameter mm 20
Min. distance back of a panel and front of the following (at 25 m/min) mm 500
Inverter Included
Minimum panel overhang mm 30
Tools provided Excluded
Tool heads N 2 included
(Select requested tool)
With this device associated with cod. N0000278 the maximum panel overhang becomes 70 mm.
SPRAYING LIQUID APPLICATION UNIT
Device for the application of liquid using nozzles located above and below the panel. It can be used with the following liquid types:
Anti-adhesive liquid. Anti-static liquid.
Cleaning liquid.
Manual adjustment of nozzle direction.
REMOVING/SLIDING LIQUID
Avoids damaging on the surface of very sensitive edges (acrylic, aluminum) due to contact with the copiers. Moreover, on edges coated with protective plastic film, this liquid prevents it from being damaged or removed during machining operations.
EDGE SCRAPER UNIT RB40
Unit comprising 2 independent carriages, which are complete with horizontal and vertical copiers and swings on slides.
Vertical movement of the top unit associated with the belt presser. Continuous automatic adjustment of tool position with respect to the material using 4 brushless motors applied to the group drive.
The position is controlled directly by the machine control system.
In this way it is possible to use multiprofile cutters on the unit, allowing the profile/shape to be changed without having to change the tool.
Automatic pneumatic disabling of the unit from the control panel.
TECHNICAL DATA
Description Um Min Max
Tool radius mm 1 3
Dust hood (diameter) mm 100
Tools provided Excluded (Select requested tool)
PRO-NESTING KIT FOR RB30, RB40
Equipped with 2 bearing copiers in addition to the top vertical copier to permit processing of panels with holes up to diameter max. 35 mm and/or grooves. Distance between copiers 100 mm.
PAIR OF MULTIPROFILE CUTTERS FOR RB30/RB40, BEVEL 25° - R=1/2/3
GLUE SCRAPER UNIT RC20
It allows to remove any glue excess from the flat surfaces of the panel close to the edges. The unit is equipped with 3+3 vertical copiers with bearings.
Equipped with suction hoods.
Complete with spraying device for tool cleaning. Automatic exclusion of the unit.
SUPERIMPOSED OSCILLATING BUFFERS UNIT SZ30
The unit includes 2 motors.
The buffer's position is adjusted by an exclusive 3D recording device by means of a ball joint.
The motors are fitted on a single column and are axially offset from one another to allow pneumatic insertion and removal of the brushes and the pneumatic swing motion that optimises wear on the brushes themselves. Vertical movement of the top motor is coupled to the presser to provide automatic adjustment according to the thickness of the panel.
The unit is supplied complete with fabric brushes. Automatic disabling of the unit when motors are stopped.
TECHNICAL DATA
Description Um Min Max
Brush rotation speed RPM 1.400
Motor size kW 0.37+0.37
Shaft (diameter x length) mm 20x40 Brush dimensions (diameter x width) mm 150x40
N0000136 1
SPRAYING LIQUID APPLICATION UNIT
Device for the application of liquid using nozzles located above and below the panel. It can be used with the following liquid types:
Anti-adhesive liquid. Anti-static liquid.
Cleaning liquid.
Manual adjustment of nozzle direction.
CLEANING LIQUID
Allows the brushing unit to remove any glue waste on the panel surface.
EDGE HEATER PH10
Allows the edge of the panel to be heated as it passes through the unit, restoring the original colour in the case of materials (PVC) that are subject to changes in colour when they come into contact with the cutter blades during profiling.
N0001304 1
2D FIXED BAR-CODE READER LOOP SOFTWARE MANAGEMENT
2D fixed bar-code reader at the machine infeed, to select the production working list by numerical control. The operator can select the bar-code reader to be used directly by numerical control.
N0000300 1
AIR CONDITIONING SYSTEM FOR STREAM B/B MDS 1.1
N0001105 1
INDEPENDENT UNITS CONTROL SOFTWARE
When machining panels with the same thickness, this software allows to change the settings of a working unit, without waiting that the previously worked panel has completely gone out of the machine.
Panel gap between the panels that have different machining requirements, varies depending on the working unit involved in the change.
SINGLE-SIDED MACHINE STREAM B
Possible working changes:
Change edge thickness/edge colour. Change from a 1st run to a 2nd run. Change milling/ grooves.
On/Off working units.
DOUBLE-SIDED MACHINES STREAM C
Possible working changes:
Change edge colour (with same thickness). Change milling/grooves.
With this optional it is possible to change the above mentioned processing, simply by stopping (STOP) the line of the WORKING LIST previously saved in the machine control by the operator: the machine will automatically conform itself to the next line.
It is possible to improve the management of this device, by a manual bar-code reader or by a line supervisor.
* All Descriptions, Specifications and Features are correct to the best of our knowledge. Interested buyers should verify before purchasing. Buyer is responsible to make sure all local regulations for installation and use are followed for area in which it is being installed. Govenment regulations may differ, depending on location.