2013 *SOLD* Edgebander - Biesse Akron 1320
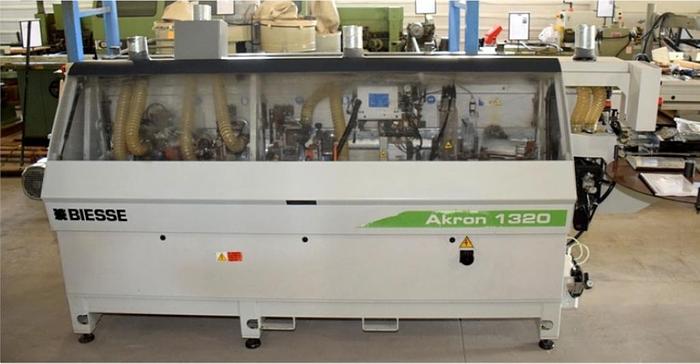
2013 *SOLD* Edgebander - Biesse Akron 1320
Location:Uxbridge, Canada
Description
Specifications
Manufacturer | Biesse |
Model | Akron 1320 |
Year | 2013 |
Condition | Used |
Stock Number | 1798BM |
Electrics | 380/400 V / 3 Ph / 60 Hz (with transformer for 600V if needed) |
Weight | 2650 lbs |
Shipping dimensions | 12'L X 3.5'W X 5'H |
Condition info | Very Good |
Additional Features
Panel height: 10-60 mm
Height of edge-banding material: 14-64 mm
Thickness of edge-banding material in rolls: 0.4-3 mm
Thickness of edge-banding material in strips: 0.4-3 mm
Panel protrusion from track: 25 mm
Min panel length: 150 mm
Min panel width (with length 150 mm): 85 mm
Min panel width (with length 250 mm): 50 mm
Track feed speed: 12 m/min
Dust extraction system for each operating unit 1 hood Ø: 100 mm
Pneumatic connection: 7 bar
Control voltage: 24 V - DC
Static frequency inverter: 200 Hz
Glue pot capacity: approx 2 Kg
Glue pot heating time at ½ load: approx. 10 minutes
Control system:
Selectors to enable working units.
Control board at the in-feed of the machine.
It includes 2 displays for the managing and displaying of the temperature of the glue pot and the glue roller.
Structural components:
Conveyor Track: it uses an industrial chain with pads realized in special self-lubricating techno-polymer. The pads slide on two guides, one with a circular section and the other one flat, complete with grease nipples. The panel being edged is held by special low wear rubber pads with a high friction coefficient, which are individually interchangeable.
Gear motor: for feed chain driving with 12 meter/min working speed.
Top presser beam: with high rigidity, allows the change of the panel thickness without set-ups on the operating units. The panel being edged is held in position by a double row of staggered wheels mounted on bearings. The top working units are hooked to the top presser and adjusted automatically with the positioning of the presser itself. The top presser beam movement is manual and centralized.
Lateral panel support: it includes extruded aluminum guide complete of support wheels.
Protection booth.
OPERATING UNITS:
C1501001 PRE-MILLING UNIT RT02
Rectifies the surface that has to be edged before applying the glue.
Complete with 2 high frequency motors (1,8 kW each) at 12.000 rpm (tools not included).
The machining of the pre-milling unit ensure a chip-free finish thanks to:
independent automatic temporized intervention of the two motors.
AUTO-SET device:
ensures optimum positioning of the cutters according to the thickness of the panel being machined.
Pair diamond-coated cutters H = 65 mm (E4000218)
C1801002 ANTI-ADHESIVE UNIT ADZ02
The unit applies an anti-adhesive liquid on the top and bottom surface of the panel to ease a good cleaning of the workpiece being processed. It is positioned on the machine before the pre-milling unit.
The anti-adhesive liquid is applied with precision by means of injectors controlled by the NC.
GLUING UNIT SP03
Applies the hot melt glue on the panel, feeds the edge to be applied to the panel being machined, automatically cuts the rolls of edge-banding material to length and presses the applied edge ensuring that it adheres perfectly to the panel.
It includes:
Glue pot and glue spreading roller: the spreading roller is complete with a copying system to apply the correct amount of glue to the panel. Manual device for the quick exclusion of the glue pot. Quick heating and double thermostat for differentiated temperature control. The glue pot is completely coated with non-adhesive material. Automatic glue temperature lowering in the glue pot when the machine has been idle for a set period of time.
Quick change of the glue pot for an easy maintenance or change colour/type of glue.
Edge feeding system: it is automatic for edges in rolls and manual for edges in strips, complete with roll holder disk.
Cutter knife: for the automatic cutting of edge-banding material in rolls with a maximum thickness of 3 mm and with a maximum section of 140 mm².
Edge pressing system. Consisting of:
a first motorized roller, diameter Ø90 mm.
an idle roller, diameter Ø60 mm.
END TRIMMING UNIT IT03
Carries out the trimming of edge excess at the front and rear part of the panel.
Complete with 1 high frequency motor (0,8 kW) at 12.000 rpm with saw blade.
Pneumatic device with pre-selection of straight or tilted cut of the edge from control panel
FINE TRIMMING UNIT RF02
Carries out top and bottom fine trimming of the glued edge. Complete with 2 high frequency motors (0,65 kW each) at 12.000 rpm, suction hood and front and vertical rotating disk copiers.
Pair of multiprofile cutters for fine trimming unit: chamfering 25 degrees, R=3 mm, straight profile for solid wood (C2004002)
C1506001 EDGE SCRAPER RB02
Finishing unit for thickness PVC/ABS edge material (e.g. 2 mm). Complete with vertical and horizontal self-cleaning rotating front and vertical disk copiers.
Standard accessories include compressed air blowers on the copiers and chips collection box. Pair of knives R=3 mm, for edge scraper (C2006005)
C1507001 GLUE SCRAPER RC02
Finishing unit to remove the exceeding glue in the junction panel-edge. Complete with turning discs copying device and flat blade knifes with timed intervention.
It includes as standard nebulized liquid for the tools cleaning and dust extraction kit.
C1508001 BRUSHING UNIT SZ02
To carry out the cleaning and polishing of the applied edge using cloth disc brushes. The unit is self-adjusting to the panel height. Complete with two 0.37 kW motors at 2800 rpm
400 VOLT, 3 PH (COMES WITH TRANSFORMER TO 600 VOLT) CSA APPROVED
COMES WITH ALL MANUALS AND EXTRA TOOLING AS SEEN IN PHOTOS